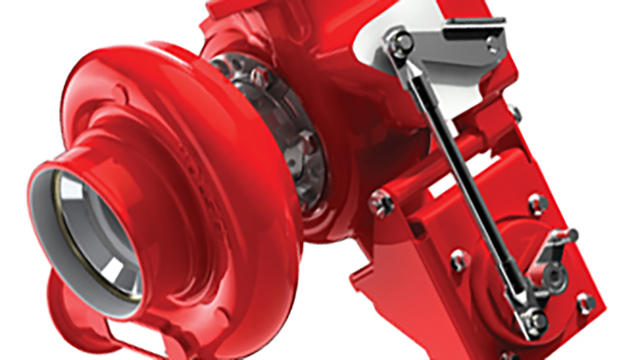
Our online stores are always open to meet your needs.
Diamond Diesel |
Ebay | Amazon
March 11th, 2018 9:49 pm
With the recent shift in industry focus from emission driven regulations to fuel economy and efficiency improvements, there has been a lot of focus on how next generation technologies are providing solutions. With this emphasis on the term ‘Next Generation’ it is often easy to lose sight of the fact that we are not necessarily talking about new technologies but enhancements and improvements to existing often simple technologies. The Electric Wastegate Turbocharger is a perfect example of this.
The concept of wastegating is almost as old as turbocharging itself. Infact some of the first 1940s aircraft engines featured electrically operated wastegates, such as the Wright R-1820 on the B-17 Flying Fortress. As it was before the age of computers, they were entirely analog and the pilots had a cockpit control to select different boost levels!
The first production passenger cars fitted with turbochargers had wastegates, these being the Chevrolet Corvair Monza and the Oldsmobile Jetfire, both launched in 1962. Passenger car use of turbochargers did not pick up again until the 1970s and heavy duty vehicles followed suit in the 1980s with the highest power ratings needing a wastegated turbine.
Most of the early wastegates used a poppet valve and Cummins Turbo Technologies developed such a design, although the final solution was to develop a flap valve that was remotely actuated from the hot turbine. The Holset WH1C was our first wastegate turbocharger, which was used on Cummins and Paccar engines in the USA in the 1980s.
Wastegate turbocharging
Wastegate turbocharging provides a simple but effective way to control the turbocharger speed and boost pressure, improving boost capability at low engine speeds.
A wastegate turbocharger uses a relatively small turbine to provide good boost at low engine speeds, but the turbocharger speed is controlled to a safe level with a wastegate valve. When the desired boost pressure is reached, the wastegate valve opens to allow a percentage of the exhaust gas to bypass the turbine wheel and go directly to the exhaust pipe. This controls the speed of the turbine so the turbocharger can provide a higher boost pressure even when the engine is operating at low engine speeds. It offers a cost-effective, reliable and durable solution for low to mid-power range engines.
To meet today’s engineering challenges, Cummins Turbo Technologies has developed an advanced wastegate turbocharger that is electrically actuated - a solution that is capable of improving fuel economy and efficiency of the modern diesel engine!
Electric actuation
The Electric actuator enables a more accurate control of the air flow through the wastegate valve than the pneumatically controlled wastegate. It allows full control over the entire load/speed range enabling fine tuning of air fuel ratio and turbine outlet temperature. This allows optimisation of emissions and fuel consumption in conjunction with aftertreatment management. At altitude Electric Wastegating in conjunction with appropriate sensors enables the Electronic Control Unit (ECU) to control the turbocharger speed, maximising the torque and hence vehicle performance at altitude.
The electric wastegate technology developed by Cummins Turbo Technologies is suitable for a range of light to heavy duty engines (3 – 16 litres) and has been engineered to increase the fuel efficiency of a modern diesel engine. With a faster response and more precise control, it helps improve engine performance, fuel efficiency and emissions. The wastegate turbocharger offers two electric actuator solutions, both with valve position feedback, for different applications:
1) For heavy duty applications we offer a robust durable solution comprising of a ‘Smart’ powerful turbine mounted actuator with brushless motor for maximum durability, water cooling for resistance to harsh thermal environments and CAN communication to interface with the latest engine control technology.
2) For light duty applications we offer a durable but cost-effective passive solution comprising a latest generation brushed motor in conjunction with a multi stage gearbox and position feedback. The assembly is compressor mounted to minimise thermal exposure.
Electric Wastegate for heavy duty applications with a 'Smart' powerful turbine mounted actuator | Electric Wastegate for light duty applications with a durable, cost-effective compressor mounted actuator | |
![]() |
![]() |
These actuators are used in conjunction with a wastegate valve and linkage mechanism developed using the latest wear evaluation and measurement techniques to ensure that they match the durability of the associated actuators and meet the duty cycle requirements. With its fast response and precise control at all areas of the engine performance envelope, the electric actuator helps to improve performance and reduce emissions to meet the stringent targets of the market.
Patented twin port wastegate technology
Cummins Turbo Technologies’ Electric wastegate also offers a twin port wastegate system option that allows gas
Patented twin port wastegate technology uses an arrow head design |
![]() |
to bypass the turbine wheel from both volutes on twin entry housings. This Patented twin port wastegate technology uses an arrow head design that gives greater durability and robustness through good sealing when valve is closed, equal opening of both ports and resistance to wear. It benefits engine downsizing and down speeding as dual ports are required to achieve high bypass flow with twin volute Turbine Housings and enables optimised aftertreatment operating conditions for emissions control.
The pioneering twin port wastegate technology is exclusive to Cummins Turbo Technologies and was developed at our Technical Centre and manufacturing plant in Huddersfield, UK. It is the first of our suite of next generation technologies, post Euro6 and EPA 13, which has moved into field testing and we are currently working together with large OEM customers to bring us one step closer to production of this advanced technology.
Next Generation Technology
Known in the industry for being the experts in variable geometry turbocharging, this latest development in wastegate technology shows Cummins Turbo Technologies continued commitment to developing the latest technologies across its entire product portfolio.
Next Generation HE300VG | Holset M2 Two Stage System with RTC |
Electric Waste Heat Recovery Turbine Expander |
||
![]() |
![]() |
![]() |
Cummins Turbo Technologies recently unveiled other solutions and next generation innovations capable of improving the fuel efficiency of modern diesel engines by at least 10%, whilst also giving the customer a diverse range of technical options to help achieve the next stage of legislation. These near market solutions, reflect the changing priorities of global engine and vehicle manufacturers and include the Next Generation HE300VG, the Holset M2 Two Stage System with Rotary Turbine Control (RTC), and the Electric Wasteheat Recovery Turbine Expander.